The Oracle Warehouse Management (WMS) rules engine provides a repository for restrictions and business policies related to your warehouse. You define and implement rules, directly from standard Oracle Applications forms, without having to write custom code. Instead, you can compose rules, by selecting various elements from lists of values. Special security features have been included in the rules engine to prevent modification of rules that are currently in use.
Rules Engine Capabilities and Rule Types
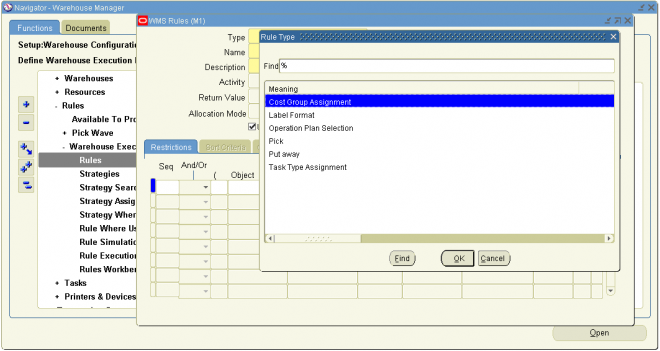
- Enables directed picking - Directed picking
- Enables directed put away - Directed put away
- Assigns cost groups to received material - Cost group assignment
- Assigns tasks to a resource with the appropriate training and equipment - Task type assignment
- Determines which operation plan will be used for consolidation - Operation plan selection
- Ensures customer compliant labeling - Label format assignment
Put away rules directs operators to put newly received material into the most appropriate location. You can base the rule on virtually any business process, and the rules engine provides intelligent suggestions for put away locations for the material. Some typical processes that put away rules are capable of modeling include the following:
• Direct an operator to put away an item in the same locator where other quantity of the item already resides. This minimizes item fragmentation.
• Prohibit commingling of different items or different lots of the same item in a single locator
• Avoid lot commingling in a locator
• Base the put away location on inspection results, the type of purchase order, or item category
You can also use the rules engine to suggest locations to put away any item anywhere within the warehouse.
Picking Rules
Directed picking creates material allocations and directs operators to pick material from specific locations. To ensure proper stock rotation, you can set up picking rules to allocate material using FIFO (First In, First Out) or FEFO (First Expired, First Out). You can also set up the rules engine to meet customer requirements, such as stock conditionor quality. Furthermore, you can set up different rules to deplete a locator to free up additional warehouse space, or to pick by cost group ownership for particular customers.
Task Type Assignment Rules
Based on user-defined criteria, such as the source subinventory, locator, or item attributes, the rules engine can identify the task type for each task that is generated by the system.
Task type assignment captures the skill sets and equipment required for a warehouse task, ensures the system assigns the task to the appropriate operator . An operator can sign onto a mobile radio frequency (RF) device, and optionally specify the equipment they are using. Based on the operator skill set, the equipment requirements, and the equipment capacity, the rules engine can then assign tasks to the operator. In some cases, the system assigns tasks based on the subinventory in which the task occurs.
For example, the rules engine assigns hazardous tasks to personnel who have completed hazardous material handling training. Another task assignment example, might include limiting put aways to top racks to those operators who signed on to a high-reach forklift.
Cost Group Rules
Cost groups capture the material valuation accounts necessary for tracking inventory value. For example, you might set up different accounts for refurbished versus new goods, or for consigned goods that might have cost groups that are tied to the owning company. When material is received into the warehouse, the rules engine can automatically determine the owning cost group.
The rules engine automates cost group assignment decisions, thus removing the complexity of making this decision from the warehouse floor. For example, the rules engine can make a cost group assignment based on sales channel by assigning different cost groups to internet orders and in-store orders. The rules engine can also make a cost group assignment based on inspection results. It can assign an item that fails inspection to a "Hold" cost group. The rules engine can also assign cost groups by vendor site, item category, item. If you do not assign a cost group rule for a particular item, then the system uses the default cost group of the storage subinventory where the item resides.
Label Format Assignment Rules
The rules engine selects the appropriate label format and content for the business need. With the compliance labeling feature, labels with the required information, bar-code symbols, and layout can be generated for each item and container.
Operation Plan Selection Rules
Consolidation is the process of bringing material from various parts of the warehouse together. Operation plan selection rules correspond to the three modes of consolidation:
LPN, Locator, and LPN and Locator. There are three types of operation plans, inbound, crossdock, and outbound. You use these plans to build the operation plan selection rules. You also use operation plan selection rules to determine if you can consolidate material across outbound deliveries. Oracle Warehouse Management allows you to create inbound and crossdock operation plans.
You cannot create outbound operation plans. Oracle Warehouse Management is seeded with the following outbound operation plans:
• LPN based consolidation in staging lane within delivery
• Direct consolidation in staging lane across deliveries
0 comments